Power Supply Issues and Faulty CNC Drives: The Relationship
- CNC Service Company
- Apr 7
- 5 min read

Power supply stability is critical in ensuring CNC drives function properly. Even minor fluctuations or inconsistencies in power delivery can lead to significant performance, reliability, and machine lifespan challenges.
Technicians, maintenance supervisors, and engineers working closely with CNC systems daily must understand the relationship between power supply issues and faulty CNC drives. It isn’t just a technical necessity—it’s a fundamental part of protecting operational efficiency and minimizing downtime.
How Power Supplies Are the Lifeline of CNC Drives
Power supplies deliver the energy CNC drives need for motion control and other essential functions. Stable voltage and current are critical for reliable operation, especially in precision-driven systems like Haas servo drives used in manufacturing and fabrication.
Voltage fluctuations can overload circuits and damage components, while insufficient power may cause motor stalls or incomplete operations, leading to defects and increased scrap rates. A sudden voltage drop can also stall a CNC machine mid-operation, exposing operators to potential hazards as the system attempts to recover. Additionally, power surges can overheat components, increasing the risk of electrical fires or equipment malfunctions.
Signs Power Supply Issues Might Impact Your CNC Drive
Diagnosing power supply-related problems in CNC systems requires close attention to equipment warning signs. Engineers and operators should be keenly aware of unusual behavior, as seemingly minor anomalies can point to larger issues within a drive system.
Telltale signs include erratic motor movements, reduced responsiveness, or error codes hinting at electrical inconsistencies. Specifically, Haas servo drives often feature error reporting systems that notify operators of problems, such as undervoltage or overcurrent errors, tied directly to the power supply.
However, interpreting these signals accurately is critical. Misdiagnosis can lead to unnecessary component replacements or leave systemic problems unresolved. Experienced technicians with the right diagnostic tools can bridge the gap between observation and resolution.

How Power Surges Impact CNC Drive Systems
Power surges are among CNC drives’ most harmful power supply issues. They often occur due to grid disturbances, lightning strikes, or poor grounding within the facility. When high voltage suddenly overloads a circuit, sensitive drive components like transistors and capacitors can suffer immediate and irreversible damage.
For example, drives used in high-performance setups often involve intricate circuits designed to deliver incredible precision. Surges that breach the intended tolerance levels can create cascading failures within the system, resulting in costly downtimes and repairs. Engines controlled by CNC drives may experience uncontrollable or erratic motions as a result, jeopardizing both final product quality and operator safety.
The Role of Power Quality in Preventative Maintenance
Proactively safeguarding CNC drive systems against power instability is not a one-time expense—it’s an essential investment in operational longevity. Routine maintenance should involve measures to monitor and improve power quality across facilities.
Step one is obtaining constant voltage and current measurements to identify any irregularities in the supply. Engineers may also consider installing voltage regulators, surge protectors, and backup generators to create a more robust distribution framework. Implementing uninterruptible power supplies (UPS) can safeguard facilities that rely heavily on systems like Haas servo drives.
Voltage Sags and Long-Term Impacts on Components
Unlike power surges, voltage sags are shorter-lived but can be just as damaging to CNC drives. When incoming voltage dips below the drive’s operational tolerance window, performance diminishes, and the system struggles to execute its intended purpose. Voltage-driven stress on integral drive components builds over time, weakening their reliability and accelerating degradation.
Motor drives, for instance, may exhibit reduced torque capabilities during voltage sags and ultimately fail to meet programmed requirements. These events may also compromise data logging and analysis systems within modern CNC platforms, obscuring performance metrics vital for continuous improvement initiatives.
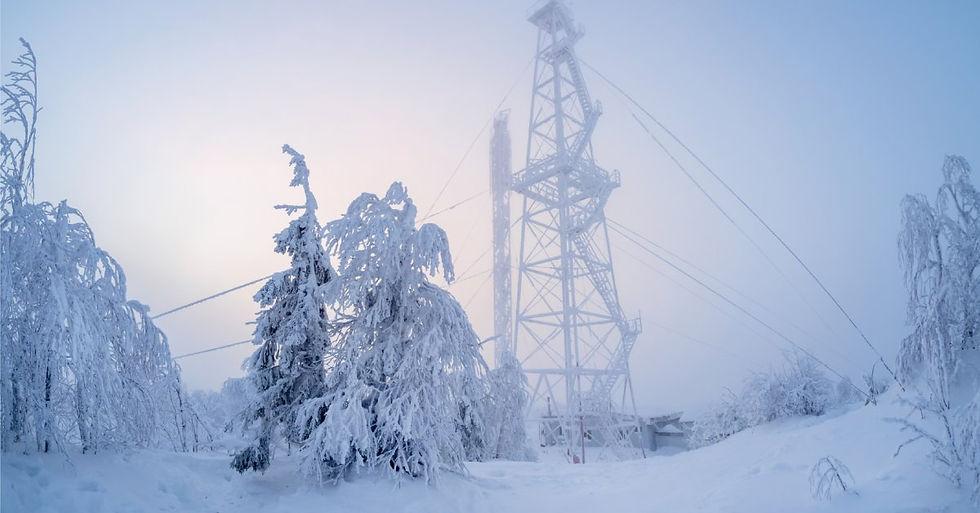
Environmental Factors Tied to Power Supply Challenges
External factors like facility location, electrical infrastructure, and environmental conditions play a crucial role in power supply challenges. Coastal areas or high-humidity zones increase the risk of corrosion, potentially damaging electrical components. Regions prone to extreme weather, such as hurricanes or heavy snowfall, face frequent power outages and grid instability, which can disrupt CNC operations and cause unexpected downtime.
Facility managers should collaborate with engineering teams to assess these risks based on their environments. For example, factories in storm-prone areas might require surge protection systems, while those in coastal regions may benefit from corrosion-resistant enclosures. Identifying these hazards early enables infrastructure improvements that help prevent issues like short circuits, voltage fluctuations, or current spikes.
The Importance of Proper Grounding for CNC Drives
Proper grounding is among the simplest yet most overlooked aspects of an effective power supply. A solid grounding system ensures power flows efficiently and safely throughout CNC systems, avoiding erratic surges or distribution issues that might compromise drive health. Without stringent grounding measures, stray voltages impact operational consistency, gradually wearing out high-sensitivity components.
Additionally, effective grounding practices also mitigate the risks of static discharge events. While seemingly trivial, static electricity can cause catastrophic failures within microcircuitry layers embedded in CNC drives, especially when paired with infrequent electrical inspections.
Repairing CNC Drives Damaged by Power Fluctuations
When CNC drives suffer damage from power issues, the repair process often requires considerable expertise and precise diagnostics. Technicians must determine whether damage stems from specific components such as semiconductors, resistors, or the cooling systems supporting them. Only then can they proceed to recalibrate or replace damaged parts.
Successful drive repairs often depend on restoring the damaged machine and rectifying the causes behind power supply issues. Small businesses operating CNC machines with limited access to internal engineering resources might benefit from third-party diagnostic services specializing in comprehensive drive overhaul and recalibration.
Why Partnering With Experts Is Critical
Reliable CNC system performance often hinges on collaborative efforts between machine operators and qualified engineering partners. This is particularly true in ensuring essential components like power supplies and servo drives remain within optimal tolerance.
For industries utilizing Haas servo drives, expertise is even more important because of their precision requirements and reliance on detailed configuration oversight. Organizations should seek repair partners with proven track records in diagnosing and resolving power-related faults while actively contributing to preventative maintenance frameworks.
Mitigating Risks With Resilient Solutions
Building resilient processes and understanding the relationship between power supply issues and faulty CNC drives shows a commitment to operational excellence. For small business owners with tight budgets, it’s essential to balance short-term costs with long-term benefits. Investing in power stabilization tools can drastically reduce failures, minimize downtime, and improve workplace safety, offering a return on investment that far exceeds the initial expense.
Power supply disruptions can cause hidden issues that escalate quickly, leading to burnt-out components or sudden motor failures. Addressing power-related problems promptly is crucial to preventing costly downtime and ensuring the long-term reliability of your CNC systems.
Additionally, to maintain peak productivity and prevent costly equipment breakdowns, businesses should address early warning signs and seek expert guidance when needed. Partnering with a trusted CNC Service Company ensures reliable power distribution, optimized machine performance, and long-term operational success. Contact us today to safeguard your CNC systems and keep your operations running smoothly.
Comments